Untransformed
The push for EVs and renewables is fueling transformer shortages and “staggering” increases in utility product costs. Consumers will be stuck with the bill.
Electricity prices are soaring.
But prices for the hardware needed to deliver electricity to homes and businesses are increasing faster than the price of the juice itself. That means consumers will be paying even higher electricity prices in the years ahead.
As can be seen in the graphic above, the inflation rate for utility products over the past two years has been 2.6 times higher than what has been seen in the economy as a whole. But the problems in the utility product sector go beyond cost. Transformer manufacturers can’t keep up with booming demand and lead times for some transformers are being measured in years. Furthermore, a proposed federal efficiency rule for distribution transformers could result in even higher prices, longer lead times, and decreased grid reliability, all at the same time climate activists and dark-money NGOs are pushing efforts to “electrify everything.”
First, some background.
Last year, U.S. all-sector electricity prices jumped by 12.5%. In some states, prices rose even faster. (California’s rates were up by 14.4%, Oklahoma’s were up by 18.2% and Maine’s all-sector electricity prices soared by 26.1%.)
But those 2022 price increases are likely only a soupçon of the price surges to come. While overall inflation in the U.S. economy was 8% last year, the cost of utility products—a host of items ranging from pole-mounted transformers and copper wire to anchor bolts and wood poles—soared by 18%. And that inflation came on top of the 2021 increase of 14%. Thus, utility product costs have risen by 34%, or more than twice the inflation rate across the U.S. over the past two years.*
These enormous costs increases are being driven by federal appropriations including those made under the Inflation Reduction Act, which contains a myriad of subsidies for alternative energy that could cost as much as $1.2 trillion, along with the Infrastructure Investment and Jobs Act, which allocates another $95 billion for EVs and grid-related spending. These laws, and state-level mandates that require the use of alternative energy, along with forced electrification measures, are fueling an unprecedented surge in demand for commodities and utility products.
This tidal wave of cash is straining supply chains and leading to huge price increases in everything from single-phase transformers to insulators. Worse yet, industry experts say there is no relief in sight. Several factors are causing these price increases including acute labor shortages, higher freight rates, shortages of specialty steel, and regulatory uncertainty over efficiency standards for transformers that were proposed in January by the Department of Energy.
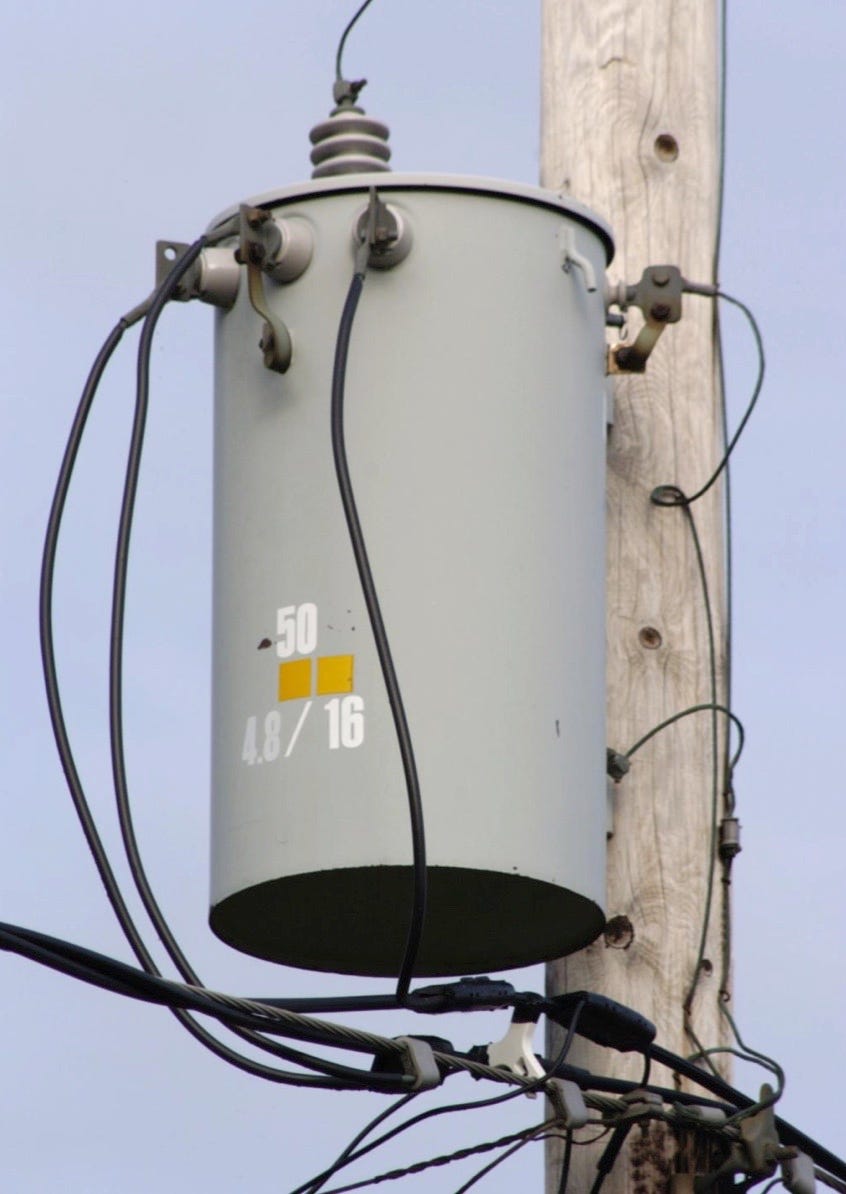
Before delving into those factors, it’s essential to remember that over the past several years, renewable energy promoters, numerous NGOs, and climate activists, have repeatedly claimed that attempting to electrify everything in our economy, from home heating and cooking to transportation and water heating will save consumers money. (See my recent piece, “The Dark Money Behind The Gas Bans.”) Or consider a recent pronouncement by London-based Legal & General Investment Management, which claimed that the cost of quitting hydrocarbons and replacing them with alt-energy technologies like solar panels and EVs was “no longer an especially relevant factor.” It also claimed that “The total economic cost when annualized over the next quarter century would be so low you would need a magnifying glass to see it.”
But those glib claims ignore the constraints in our supply chains, including the mining, metals, and manufacturing needed to provide the hardware for the electric grid. Few people understand those supply chains better than Matt Brandrup, the CEO of the Rural Electric Supply Cooperative, a Wisconsin-based coop that provides utility products to coops in the northern part of the U.S
During his appearance this week on the Power Hungry Podcast, Brandrup told me, “In two short years, everything that we sell on average, [has gone] up by about a third. That's a staggering inflationary increase in two years that in my 25 years in the business, I've never seen, even going back to the housing boom years of 2006-2007...we saw some pretty good inflationary rates on the products that we sell back then. But they were in the 7% to 8% range. So to see an almost a 33% increase in two years is pretty staggering, and quite frankly, tough on our members and non-member utilities to deal with.” In addition to big price increases on things like pad-mounted transformers––which went up by 47% in 2022––Brandrup said RESCO is seeing one- to two-year lead times on transformer deliveries.
“Demand is outpacing supply,” explains Buddy Hasten, the CEO of the Arkansas Electric Cooperative Corporation (AECC) which owns ERMCO Distribution Transformers, one of America’s biggest manufacturers of electric transformers.
During a phone call on Tuesday, Hasten told me that ERMCO, based in Dyersburg, Tennessee, can’t hire enough workers to keep up with demand. “ERMCO made more transformers in 2020 than they ever did. In 2021, we were close to the 2020 record,” he said. “But we worked so much overtime in 2021, we had 700 people quit. Since then, we’ve hired 1,000 new people. But we could hire 600 or 700 more people right now. Getting the labor to make these things has been everybody’s challenge. This is not transitory.”
We could hire 600 or 700 more people right now. Getting the labor to make these things has been everybody’s challenge. This is not transitory.”
According to Hasten, ERMCO produces about 25% of all the transformers in the country. It produced about 425,000 transformers last year. But demand still outstripped supply.
Hasten said the supply shortages go beyond distribution transformers and include power transformers, the big machines that you see in substations. “None of those are made in America,” said Hasten. Adding more high-voltage transmission he said, will require “more big transformers. The lead time on those is now two to three years. But we depend on foreign companies for all of those. That’s not an industrial strategy that says ‘national security’ to me.”
Last November, leaders of the biggest associations in the electric sector along with three construction groups, sent a letter to Congressional leaders asking them to prioritize transformer production. The National Rural Electric Cooperative Association, American Public Power Association, Edison Electric Institute, National Association of Home Builders, Leading Builders of America, and Associated General Contractors of America asked them to “appropriate $1 billion this year for implementation of the Defense Production Act to specifically address the supply chain crisis for electric distribution transformers.”
They continued, “electric utilities continue to have significant problems in procuring basic equipment––particularly distribution transformers––needed to operate the grid, provide reliable electric service, and restore power following severe storms and natural disasters. In housing construction, this is further exacerbating their ability to address the housing affordability crisis facing our nation.”
But Hasten said the federal government hasn’t responded in a significant way. In addition to labor shortages and increased freight costs, Hasten said the transformer industry is having trouble sourcing specialty steel, and in particular, grain oriented steel or GOES, a paper-thin, hard-to-manufacture metal that contains about 3% silicon by weight. (The added silicon improves the “soft magnetic” properties of the steel.)
But there isn’t enough GOES to go around. GOES accounts for just 1% of global steel production and wait times for some customers are now approaching a year. In addition to its use in transformers, GOES is used in electric vehicles, which is further straining supplies. According to a recent piece in the Wall Street Journal, China, Japan, and South Korea now produce more than 80% of the world’s supply of electrical steel. And all of those countries are subject to tariffs or quotas on steel imports. Only one company in the U.S., Cleveland Cliffs, makes GOES. U.S. Steel is tooling up a GOES plant, but it is months away from production.
Making matters worse: the future supply of GOES, as well as the manufacturing capacity needed to make distribution transformers, is being imperiled by a proposed rule that will impose higher efficiency standards on transformers even though existing transformers are about 95% efficient. On January 10, the Energy Efficiency and Renewable Energy Office at the Department of Energy posted a proposed regulation that will require manufacturers to boost the efficiency of their transformers by about 1%. But achieving that tiny gain will require retooling their factories. It will also, according to Hasten, force them to use amorphous steel. But Hasten says there are no amorphous steel producers in the U.S.
On March 7, Theresa Pugh, who heads Virginia-based Theresa Pugh Consulting, a firm that represents industry on regulatory matters, filed a comment with the DOE that blasted the proposed rule. “Distribution transformers are already regulated to meet energy efficiency,” she wrote. “Seeking the additional de minimis 1% is an incredible waste of private sector money, investment, re-design of transformer manufacturing, resulting upon reliance upon ONE steel company. Most of all it is a waste of time and makes supply chain problems worse.”
Pugh added that the measure if adopted and put into place by the proposed deadline of 2027, will likely result in a “2.5 or perhaps a 3-year wait for electric distribution transformers.” She continued, saying that homebuilders are already feeling the pinch of the transformer shortage and that the proposed rule “does not recognize that the current shortage will only become worse as the electric sector must place new distribution transformers to support electric vehicles.”
In the middle of a supply chain crisis, the federal government is saying “we are going to make this whole technology obsolete and we’re going to force you to go to a new technology that we’ve never used before.” Hasten continued, “The federal government is out of tune with the real physics of the universe.”
Hasten agrees. In the middle of a supply chain crisis, the federal government is saying “we are going to make this whole technology obsolete and we’re going to force you to go to a new technology that we’ve never used before.” He continued, “The federal government is out of tune with the real physics of the universe.”
There’s more to write about the supply chain challenges lurking in the electric sector. But it is already clear that the surging cost of utility products that is being driven by the billions of dollars in alt-energy subsidies and the electrify everything push will impose more costs on consumers and taxpayers.
The only question at this point is how big those costs will be.
* I have corrected math errors that were in my initial post. I understated the inflation rate in utility products and the U.S. over the two-year period from 2021 to 2022. The correct numbers are 34% and 13%, respectively. Further, utility product inflation was 2.6 times higher than what was seen in the economy as a whole, rather than 2.5 times as I originally stated. Thanks to Rod Adams for pointing out the error.
I’m seeing this exact thing in my industry. I work in the industrial chemical sector on the gulf coast and lead time on a 3-phase transformer bank (pole mounted) is 10-12 months! Not too long ago it was about 1-2 months and now we’re being forced to get very creative. It’s the same story with a prefabricated substation we are procuring that has a lead time of about 80 weeks. It has made my job quite difficult and will not stop if the push for electrification continues without any reality. Thanks for your reporting, sir!
Good article describing what is in store for us over the next few years. It prove once again, bureaucracy is not your friend. The overzealous scheme to save a particle of carbon at any price is the most fiscally destructive mythology our world has ever seen, better said as 'the most fiscally destruct the public has yet to grasp. If we did see it, our voting pattern might be altered a bit. And we'd see Al Gore on the comer with a tin cup.